
Case Study
Cypress Cove Equipment Replacement
OBJECTIVE
The existing cooling towers within Cypress Cove's Central Energy Plant provide cooling for the entire 48-acre campus and needed replacement to reduce energy consumption and increase system reliability. Given the imminent risk of structural failure posed by the existing old cooling tower, it was crucial to complete the installation before any breakdown occurred. As an American Health Care Association (AHCA) regulated assisted living facility, maintaining cooling operations during the installation of the new cooling tower was vital for the safety and comfort of Cypress Cove’s over 500 residents.
CHALLENGES
The Cypress Cove project presented significant spatial challenges. The cooling towers were surrounded by trees and located in a confined area with limited maneuverability. The environment warranted careful planning and precise execution, particularly when using cranes to lift and position heavy equipment. Furthermore, one of the original cooling towers exhibited critical structural issues: a fiberglass leg was breaking, the tower fans were on the verge of falling through the bottom of the unit, and the entire tower was at risk of tipping over. Addressing these urgent vulnerabilities was a top priority to prevent any catastrophic project failures.
To facilitate the installation in such a constrained space, United Mechanical employed several innovative strategies. Chiller skates were utilized to get the new pumps through the building and into the chiller plant, and a gantry was built across the pump area to lift the three old pumps out and install the three new pumps, leaving some room to complete future repairs or replacements. This creative approach allowed for the precise placement of equipment without needing extensive demolition or reconstruction of the piping systems in tight quarters.
To meet the client’s goals of longevity and reliability, United Mechanical installed stainless steel cooling towers, which offer enhanced durability compared to traditional materials, such as fiberglass. This ensured a longer lifespan and reduced the likelihood of future maintenance issues.
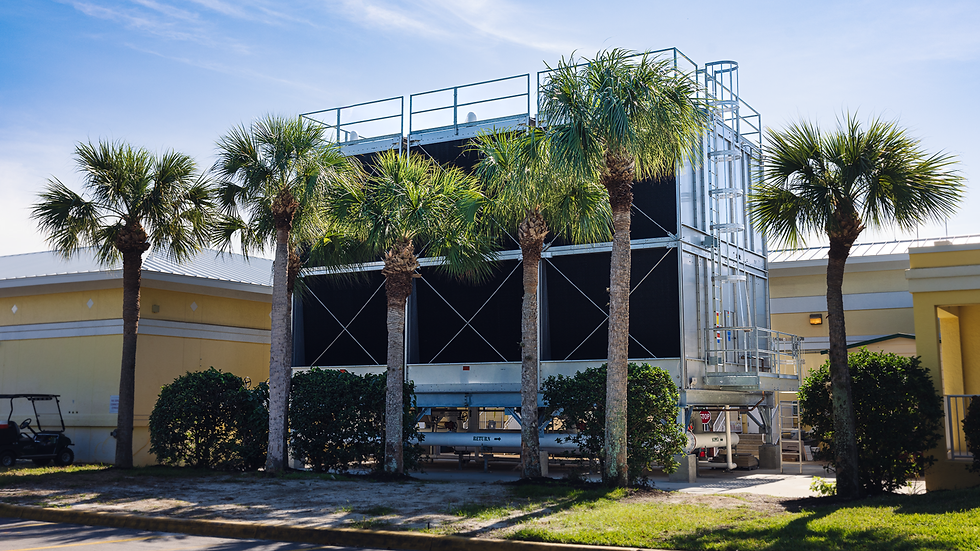

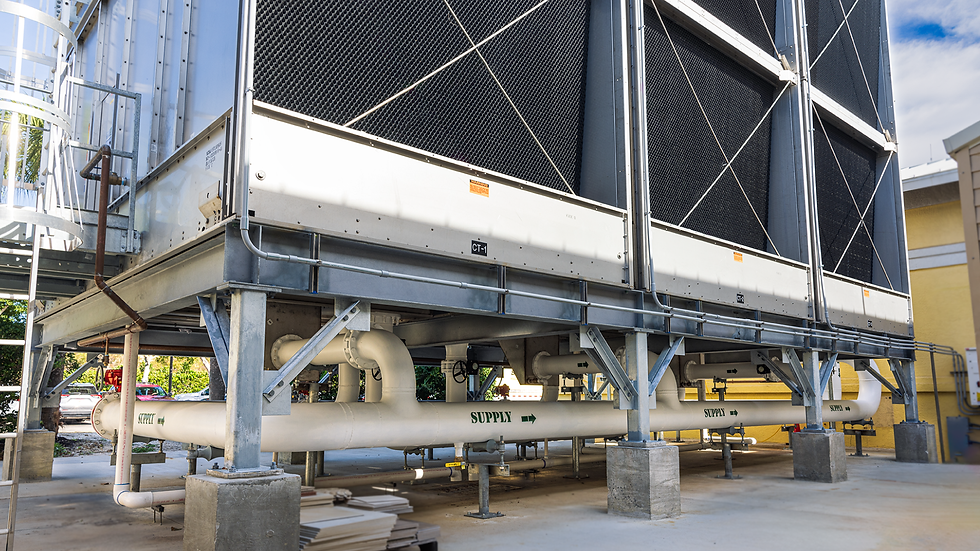
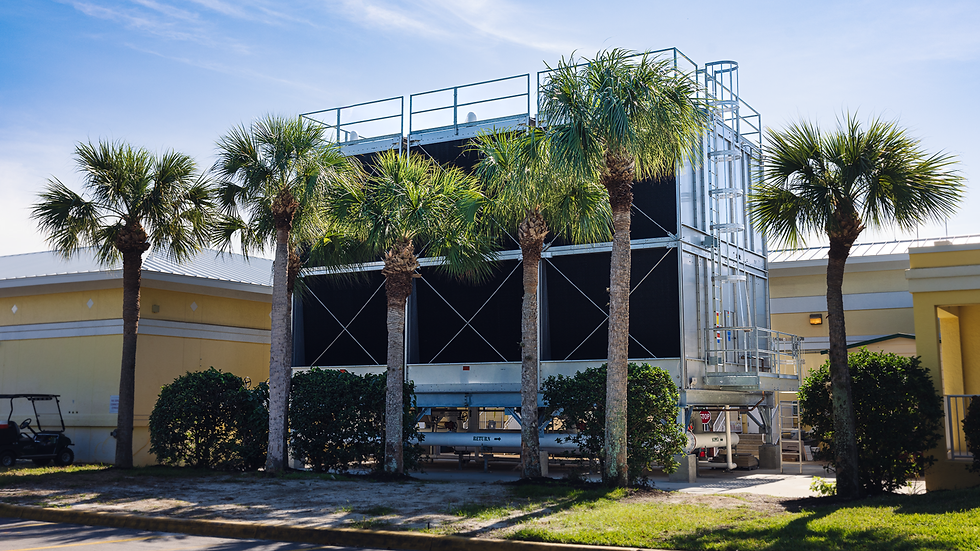
PROJECT DETAILS
Mechanical Contractor
United Mechanical
A Fidelity Company
Client
Cypress Cove
Industry
Assisted Living
Category
Equipment Replacement
BACKGROUND
Cypress Cove, an assisted living facility providing innovative senior living solutions for older adults in Fort Myers, Florida, contacted United Mechanical, a leading full-service HVAC/mechanical and Building Automation Systems (BAS) contractor, to replace the cooling towers at the facility’s Central Energy Plant.
EQUIPMENT
-
Three Cell Stainless Steel Marl Towers (NC8413TLN)
-
Alternate Tower Installed & Optimized for Full Redundancy
-
Two Running Towers
-
750-Ton Capacity Per Cell
-
1,500 Tons at 4,500 Gallons/Minute
-
-
50-Horsepower Continuous Flow Pumps
-
Variable Frequency Drives (VFDs)
-
Three for Each Tower
-
SOLUTION
Prior to installing the new cooling towers, United Mechanical conducted a thorough review of the original engineering design of the tower for Cypress Cove. The team identified opportunities to optimize the configuration, leading to significant cost savings for the client. One of the key recommendations was to simplify the piping arrangement. Initially, the design placed the piping in an area prone to moisture from cooling tower condensation, which could lead to deterioration. United Mechanical proposed relocating the piping beneath the towers to decrease exposure to moisture. This redesign not only enhanced the longevity of the piping, but sufficiently reduced the overall project cost to allow for a complete replacement of all piping components, rather than just partial replacements.
In preparation for the installation of three new stainless steel cooling towers, United Mechanical managed the excavation of the old cooling tower footers with a subcontractor. New structural footers and piers were installed to adequately support the increased weight of the new towers.
United Mechanical’s electrical division played a vital role in delivering the project by installing all Variable Frequency Drives (VFDs), conduits, and wiring for all motors and drives. Concurrently, the piping division took on extensive pre-fabrication work, which included crafting the steel structure underneath the towers and pre-fabricating all necessary steel piping and components. These components were welded in-house prior to installation — a strategy that significantly expedited the on-site installation process and resulted in further cost efficiencies.
The project also focused on ensuring the long-term flexibility and reliability of the cooling system. By rearranging the piping into a configuration that was more beneficial for the owner and incorporating prefabricated elements, United Mechanical was able to streamline the installation process and reduce on-site labor time.
A critical aspect of the project was maintaining uninterrupted cooling for the Cypress Cove campus. United Mechanical designed and implemented temporary cooling solutions, achieved through the use of temporary cooling towers, which were a cost-effective alternative to the initially planned temporary chillers at about 50% of the cost. The redesign incorporated temporary taps for both the chilled and condenser water systems to ensure a backup cooling solution — regardless of any system downtime.
United Mechanical's ability to handle the majority of the required trades using internal resources and staff proved to be a unique advantage. This off-site structural steel and piping component prefabrication meant that the time required on-site was reduced to just a third of what it would typically be. All welding and assembly of components were completed within the in-house shop, ensuring high-quality craftsmanship and reducing the complexity of on-site work.
RESULTS
The cooling tower replacement delivered both immediate and long term benefits to the Cypress Cove community. By reconfiguring the piping layout and utilizing stainless steel cooling towers, United Mechanical not only extended the lifespan of the cooling system but achieved significant cost savings. The project was executed within a tight six-month timeframe despite the challenging spatial constraints and critical structural issues.
United Mechanical’s innovative approach, including off-site prefabrication and the strategic use of temporary cooling solutions, ensured that there was no interruption to the campus's cooling services during the installation. The ability to handle most trades internally and pre-fabricate components reduced on-site labor time by two-thirds, minimizing disruptions and expediting the project timeline. These efforts culminated in a reliable cooling system for Cypress Cove, enhancing operational efficiency and resident comfort.